Isolated Double Wall /
Floor Slab Basic Version
Precast
- Mold & Rebar Preparation
- 2 Axis Concrete Casting
- Casting Bed Carriage Trolley
- Curing Area
- Turning Machine
- Tilting Table
- Storage Area
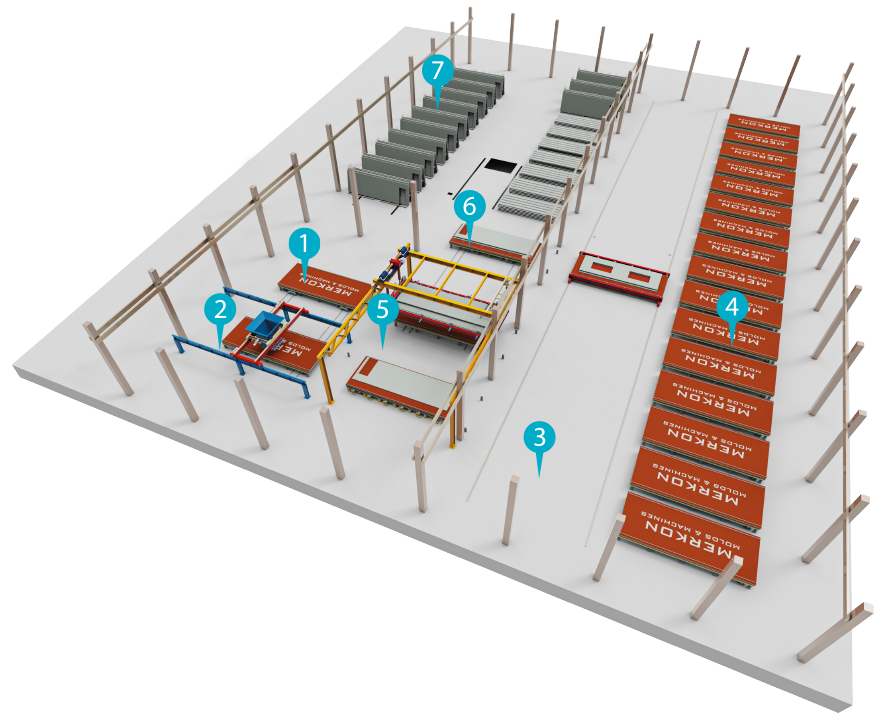
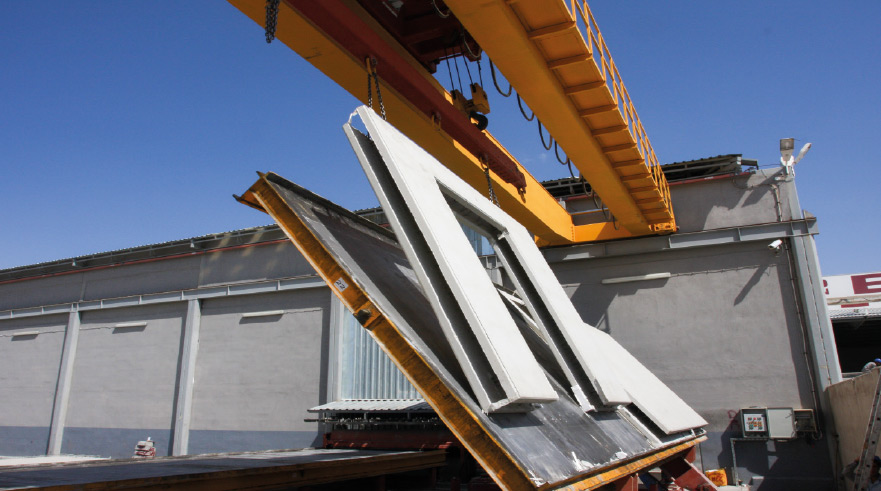
In the basic double Wall system, concrete is casted over the bed that is already divided into segments and reinforced, in the previous station, according to the project . Since the product creates a load-baring wall it is crucial to have correct casting. A special transport trolley carries the casting beds to get cured. To create a double Wall, settled concrete bed is brought underneath the turning machine, then raised, turned upside down and sticked in the freshly casted bed, before they are stored in curing area together. After both sides are cured, the Wall is tilted upwards in the last station so the products can be handled by cranes. If the Double Wall is required to be isolated, the insulation material is put on top of the freshly casted bed, before the other layer, so the lattice girder’s bars can go though it when the dried section joins in. A floor slab does not need no other processes, besides rainforcement and lattice girder placing, casting and curing.
PRODUCT DIMENSIONS | Max Lenght (m) | Max Width (m) | Max Thickness (cm) | m² on Pallet |
DOUBLE WALL / INSULATED DW | 9,5 | 3,5 | 35 | 33,25 |
FLOOR SLAB | 9,5 | 3,5 | 35 (5-6 concrete) | 33,25 |
PRODUCTION CAPACITY | PALLETS PER HOUR | PER 20 HOUR DAY | DAILY YIELD m² (80% efficiency) | YEARLY YIELD (m²) (300 days) |
DOUBLE WALL / INSULATED DW | 0,5 | 10 | 266 | 79800 |
FLOOR SLAB | 1 | 20 | 532 | 159600 |
Auto Mesh DOUBLE WALL / INSULATED DW | 1 | 20 | 532 | 159600 |
Auto Mesh FLOOR SLAB | 2 | 40 | 1064 | 319200 |